The production of fabric vertical blinds involves several steps to transform raw materials into finished blinds. Here is a general overview of the production process:
Material Selection: The first step is to select the appropriate fabric for the vertical blinds. Fabrics with suitable properties such as durability, light filtering or blocking capabilities, and desired aesthetics are chosen. Common materials used for vertical blinds include polyester, cotton, linen, or a combination of these.
Cutting: The selected fabric is cut into strips of the desired width and length, based on the measurements required for the blinds. Precision cutting ensures uniformity in the size and shape of the fabric strips.
Hemming: The edges of the fabric strips are hemmed to prevent fraying and provide a clean finish. Hemming can be done through sewing or heat sealing, depending on the type of fabric and manufacturing capabilities.
Slat Insertion: The fabric strips are then attached to individual slats. The slats are typically made of rigid materials such as aluminum or PVC. Each fabric strip is inserted into the top pocket of a slat, securing it in place. This process is repeated for each slat, ensuring uniform spacing between the fabric strips.
Welding or Stitching: If necessary, the fabric strips may be welded or stitched to the slats for additional strength and stability. Welding is commonly used for synthetic materials like polyester or PVC, while stitching is suitable for fabrics like cotton or linen.
Headrail Assembly: The headrail, which holds the slats and facilitates their movement, is assembled. The headrail typically consists of metal or plastic components that provide structural support and allow the blinds to be operated smoothly. The fabric-slatted panels are attached to the headrail, ensuring proper alignment and functionality.
Bottom Weight and Chain Attachment: A bottom weight is attached to the bottom edge of each fabric strip to maintain tension and stability. The bottom weight can be made of metal or plastic and provides the necessary weight to keep the fabric straight and taut. Additionally, a control chain or cord is attached to the headrail, allowing users to adjust the vertical blinds' position and angle.
Quality Control: Throughout the production process, quality control measures are implemented to ensure that the fabric vertical blinds meet the desired specifications. This includes inspecting the fabric for any defects, checking the alignment of the slats, and verifying the smooth operation of the blinds.
Packaging: The finished fabric vertical blinds are carefully packaged to protect them during transportation and storage. Proper packaging helps prevent damage, wrinkles, or deformation of the blinds.
It's important to note that the specific production steps and techniques may vary depending on the manufacturer, the type of fabric used, and the customization options available. The production process described above provides a general framework for the manufacturing of fabric vertical blinds.Meanwhile,Fabric vertical blinds are window coverings consisting of fabric panels attached to individual slats or tracks. The structure of fabric vertical blinds typically includes the following components:
Headrail: The headrail is the topmost part of the blind that holds and supports the entire system. It is usually made of metal or durable plastic and contains mechanisms for controlling the movement of the blinds. The headrail may include a track or channel system that allows the fabric panels to slide smoothly along it.
Fabric Panels: Fabric panels are the main components of fabric vertical blinds. They are typically made of various fabrics such as polyester, cotton, linen, or a blend of these materials. The fabric panels hang vertically from the headrail and can be adjusted or rotated to control light and privacy. The panels are attached to individual slats or tracks, allowing them to move independently.
Slat/Track System: The slat or track system provides support and guidance for the fabric panels. The slats are usually made of rigid materials such as aluminum or PVC and are spaced evenly along the width of the blinds. Each fabric panel is attached to an individual slat or track, allowing for individual panel movement. The slats can be tilted or rotated to adjust the amount of light and privacy desired.
Bottom Chain or Weights: At the bottom of each fabric panel, there may be a chain or a weight system to provide stability and tension. The chain helps to maintain uniform spacing between the fabric panels and enables the control of their movement. The weights are typically inserted into the bottom pockets of the fabric panels to keep them straight and prevent excessive swinging.
Control Mechanism: Fabric vertical blinds are operated using a control mechanism, usually a chain or cord. The control mechanism allows users to adjust the position and rotation of the fabric panels, opening or closing the blinds to control light and privacy. By pulling the control mechanism, the fabric panels can be smoothly drawn to the desired position.
Mounting Hardware: Fabric vertical blinds are installed using mounting hardware, which includes brackets or clips that secure the headrail to the window frame or wall. The mounting hardware ensures stability and proper positioning of the blinds.
Valance (Optional): Some fabric vertical blinds may include a valance, which is a decorative covering that conceals the headrail and adds a finished look to the blinds. The valance is often made of the same fabric as the panels or a complementary material.
The structure of fabric vertical blinds can vary in terms of design, materials used, and customization options offered by different manufacturers. However, the components mentioned above provide a general understanding of the structure and functionality of fabric vertical blinds.
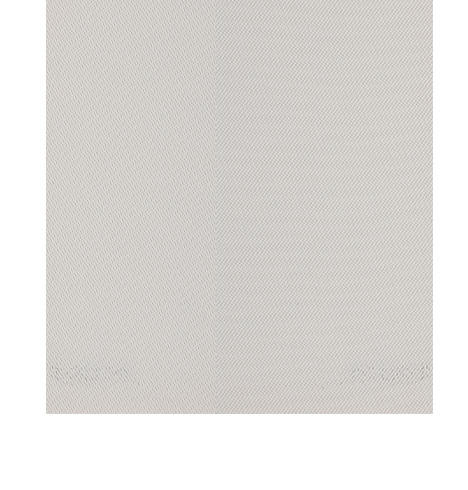
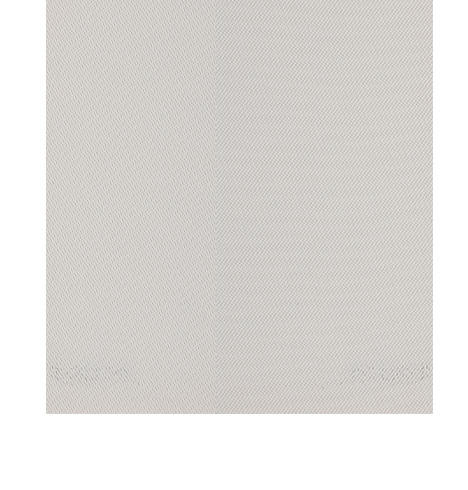