The creation of geometric patterns on roller shade fabric involves a weaving process that interlaces two sets of yarns—warp yarns and weft yarns—to form the desired geometric design. Here's a specific process for weaving geometric patterns on roller shade fabric:
1. Design Concept and Planning:
The process begins with the conceptualization of the geometric pattern design. Designers use computer-aided design (CAD) software to create a digital representation of the pattern.
2. Yarn Selection:
The choice of yarn is crucial, as it determines the colors and textures within the pattern. Manufacturers select yarns of different colors and materials to create the geometric design. For example, they may use one set of yarns for the background color and another set for the pattern elements.
3. Warps and Wefts:
Roller shade fabric production involves two sets of yarns:
Warp Yarns: These run vertically, parallel to the length of the fabric.
Weft Yarns: These run horizontally, perpendicular to the warp yarns.
4. Setting Up the Loom:
The weaving loom is prepared for the weaving process. The warp yarns are attached to the loom's warp beam, and the weft yarns are wound onto bobbins or spools.
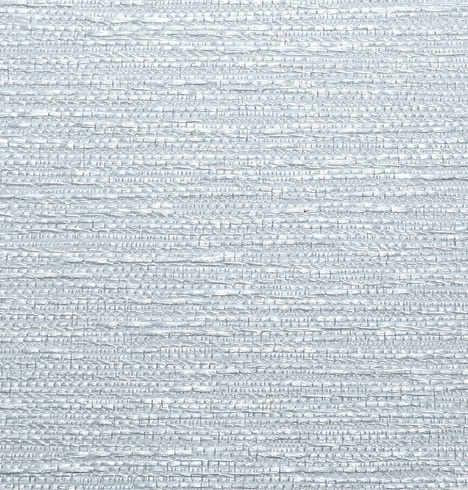
5. Pattern Drafting:
The digital pattern design is translated into a weaving pattern draft. This draft specifies how the warp and weft yarns will interlace to create the geometric pattern. Each square in the draft represents a weaving point, with different symbols indicating warp and weft positions.
6. Weaving Process:
The actual weaving process begins on the loom. The warp yarns are loaded onto the loom's harnesses and reeds, and the weft yarns are inserted through the shed (the space created between the raised and lowered warp yarns) using a shuttle or other weaving tools.
The weaving process follows the pattern draft precisely. When the weft yarns pass through the shed, they interlace with the warp yarns according to the draft, creating the geometric pattern.
As the fabric advances on the loom, the pattern repeats, forming a continuous and consistent design.
7. Tension and Beat-Up:
Proper tension on the warp and weft yarns is essential to maintain the integrity of the pattern. The weaver ensures that the yarns are appropriately tensioned.
After inserting each weft yarn, the weaver uses a reed or beater to push the weft yarn tightly against the woven fabric, compacting the threads and ensuring a uniform weave.
8. Color Changes and Combinations:
To create intricate geometric patterns with multiple colors, the weaver carefully changes the weft yarns as needed, following the color chart provided by the pattern draft.
The combination of different colored weft yarns with the warp yarns results in the desired color scheme within the geometric pattern.
The specific weaving technique used to create geometric patterns may vary depending on the design complexity and the type of loom being used. However, the general process outlined here illustrates how geometric patterns are woven into roller shade fabric with precision and attention to detail.